Do You Need a Contractor Safety Program?
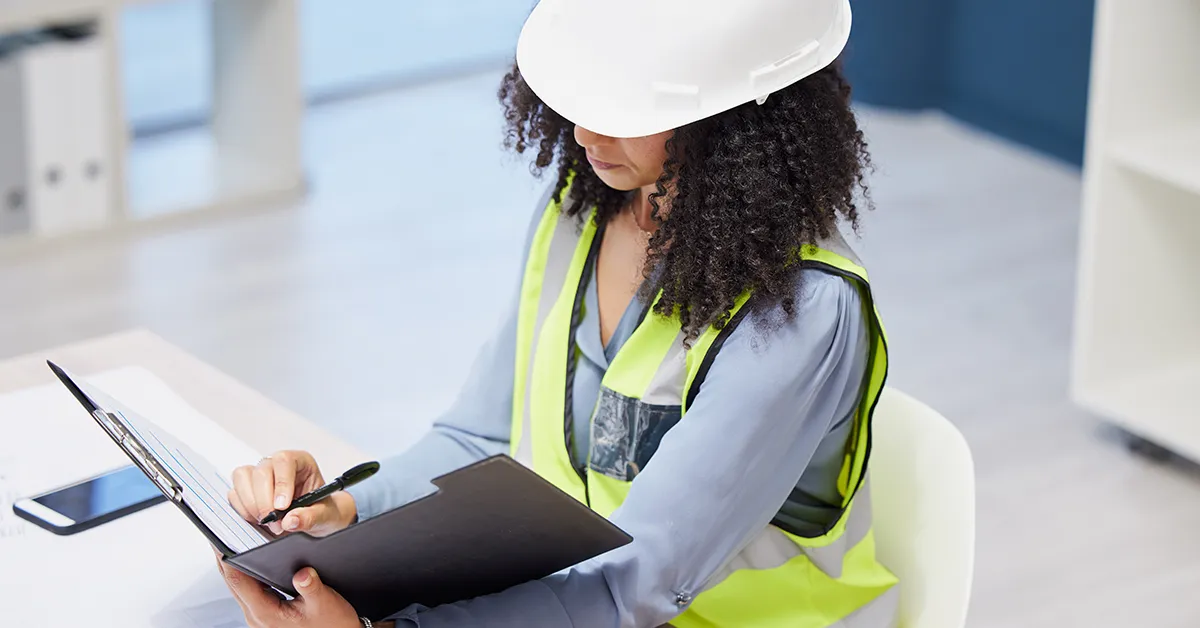
Having a contractor safety program in place provides a systematic approach to ensure contractors adhere to the same safety standards as your employees. Contractors, by nature, might be rotating through multiple job sites with varying safety cultures and regulations, which can lead to potential inconsistencies in understanding and practicing safety protocols. A contractor safety program bridges this gap by clearly outlining the safety expectations, training requirements, and compliance protocols right from the start.
In this article, we will explore what a contractor safety program entails and why it is crucial for businesses that utilize contractors.
What Is a Contractor Safety Program?
A contractor safety program is a comprehensive set of policies and procedures designed to protect the health and safety of third-party contractors working on behalf of a business, and these programs are vital for businesses that regularly utilize contractors as part of their operations.
Contractor safety programs typically include guidelines relating to risk assessment, hazard identification, personal protective equipment (PPE) protocols, and emergency procedures. They may also involve training sessions or online courses to ensure contractors understand the risks involved with their work and are equipped with the knowledge they need to stay safe on the job.
Implementing a contractor safety program can help mitigate potential accidents or injuries that could cause harm not just to workers but also to a business's reputation. By putting in place stringent safety standards for all parties involved in their operations, companies can build trust among clients while providing a safer workplace environment for all those who step onto their premises each day.
The Benefits of a Contractor Safety Program
- It Ensures a Safe Working Environment
A well-designed contractor safety program ensures compliance with industry regulations and standards and creates awareness about potential hazards in the workplace. It helps contractors understand what is expected of them when working on-site or in collaboration with your organization. Establishing procedures around orientation, training, PPE use, and emergency drills ensures that everyone involved understands how to operate safely within the facility guidelines. - It Reduces the Risk of Injury
If employees, contractors, and visitors all understand what is expected of them as they perform their work or move about the job site, the risk of accidents, injuries, and fatalities plummets. Even though contractors aren't your employees, you're still responsible for their safety. If a contractor gets hurt on your job site, you could be held liable, which may have severe consequences. - It Reduces Stress
A dedicated contractor safety program can help relieve some of the added stress of managing external resources. Contractors and companies have different needs; some may require more coaching and training than others. A contractor safety program ensures that all contractors receive the necessary training and resources to perform their jobs safely, regardless of their individual needs. - It Helps You Evaluate Contractors
By keeping track of safety incidents and creating safety reports, you can evaluate contractors and make improvements for the future. If you don't have a program in place and do not adequately track incidents, you may end up hiring contractors that previously gave you trouble.
Does OSHA Have Contractor Safety Program Requirements?
The Occupational Safety and Health Administration (OSHA) sets standards and regulations to ensure workplace safety and health in the United States. While OSHA itself does not explicitly require businesses to have a "Contractor Safety Program," it does mandate that employers, including host sites, are responsible for providing a safe and healthful workplace.
This responsibility can include ensuring that contractors working on their site are following OSHA regulations and standards. In many industries, especially in construction, manufacturing, or industrial sectors, it is common for companies to develop Contractor Safety Programs as part of their overall safety management system. These programs are designed to ensure that contractors understand and comply with the relevant safety standards and practices.
How to Perform Contractor Safety Training
Training is a vital component of any contractor safety program. It should be customized to address the specific hazards that contractors will encounter on the worksite. The training should also be designed to be clear and engaging, motivating contractors to learn and retain the information.
The initial step in providing contractor safety training is identifying the site-specific hazards and work considerations. Once these hazards and site-specific considerations have been identified, the training program can be crafted to address, mitigate, and inform your contractors.
The training program should cover the following topics:
- An overview of the company's safety program and policies.
- The specific hazards that contractors will encounter on the worksite.
- How to recognize, avoid, and control those hazards.
- How to use personal protective equipment (PPE) and other safety equipment.
- Emergency procedures and evacuation routes.
- The proper use and handling of tools and equipment.
- Reporting procedures for accidents, incidents, and near misses.
The training program should be delivered by qualified trainers with experience in the company's specific hazards and work practices. The trainers should be able to engage the contractors in the learning process and use various training techniques, such as hands-on demonstrations, videos, and interactive activities.
The 12 Core Elements of a Contractor Safety Program
Every business that uses external contractors must have a comprehensive contractor safety program in place to protect all workers involved. The process of creating an effective program starts with identifying the essential components necessary for workplace safety.
Here are 12 core elements First Choice Safety Solutions relies on to reduce injuries and incidents:
- Management Commitment
- This is the foundation of any safety management system (SMS). Senior management must be committed to safety and lead by example. Their commitment is shown by allocating resources, defining a safety policy, and setting safety objectives.
- This is the foundation of any safety management system (SMS). Senior management must be committed to safety and lead by example. Their commitment is shown by allocating resources, defining a safety policy, and setting safety objectives.
- Safety Accountability and Responsibilities
- Defines roles and responsibilities at all levels in the organization. Everyone should know what their safety responsibilities are, from the CEO to the frontline employees.
- Defines roles and responsibilities at all levels in the organization. Everyone should know what their safety responsibilities are, from the CEO to the frontline employees.
- Appointment of Key Safety Personnel
- Dedicated personnel like a safety manager or a safety committee that oversees the implementation and maintenance of the SMS.
- Dedicated personnel like a safety manager or a safety committee that oversees the implementation and maintenance of the SMS.
- Coordination of Emergency Response Planning
- Ensures that in an emergency, predefined procedures and trained personnel are available to handle the situation efficiently and safely.
- Ensures that in an emergency, predefined procedures and trained personnel are available to handle the situation efficiently and safely.
- SMS Documentation
- This consists of all the manuals, procedures, and records that support the SMS. Proper documentation ensures that safety processes are consistently applied.
- This consists of all the manuals, procedures, and records that support the SMS. Proper documentation ensures that safety processes are consistently applied.
- Hazard Identification
- A proactive approach to identify potential hazards before they result in incidents or accidents. This can involve safety reports, audits, and inspections.
- A proactive approach to identify potential hazards before they result in incidents or accidents. This can involve safety reports, audits, and inspections.
- Safety Risk Assessment and Mitigation
- Once hazards are identified, they are assessed in terms of risk, and appropriate actions are taken to mitigate or eliminate those risks.
- Once hazards are identified, they are assessed in terms of risk, and appropriate actions are taken to mitigate or eliminate those risks.
- Safety Performance Monitoring and Measurement
- Involves collecting data on safety performance, analyzing it, and comparing it against safety objectives and benchmarks.
- Involves collecting data on safety performance, analyzing it, and comparing it against safety objectives and benchmarks.
- Management of Change
- When significant changes occur in the organization (like new equipment, procedures, or personnel), it's essential to assess the safety implications of those changes.
- When significant changes occur in the organization (like new equipment, procedures, or personnel), it's essential to assess the safety implications of those changes.
- Continuous Improvement of the SMS
- An SMS is not a static system. Regular reviews and audits ensure that the system adapts to changes and improves over time.
- An SMS is not a static system. Regular reviews and audits ensure that the system adapts to changes and improves over time.
- Training and Education
- Ensures that everyone in the organization, from new hires to senior management, receives the necessary training to understand and execute their safety responsibilities.
- Ensures that everyone in the organization, from new hires to senior management, receives the necessary training to understand and execute their safety responsibilities.
- Safety Communication
- Clear and open communication channels ensure that safety information, whether about new hazards or procedure changes, reaches all stakeholders.
How to Start a Contractor Safety Program
Starting a contractor safety program is paramount for ensuring safety and efficiency on worksites, especially when multiple parties and tasks intersect. The process begins with a clear, written policy that articulates an organization's commitment to contractor safety, defining the scope, standards, and responsibilities for all parties involved. Before onboarding, contractors should undergo a rigorous prequalification process, including background checks and verification of their past safety performance. Once on site, contractors need a comprehensive orientation, highlighting site-specific hazards, equipment training, and emergency protocols.
Continuous monitoring and supervision are essential, with regular audits, safety meetings, and an established incident reporting mechanism. Effective communication channels, including feedback loops and safety bulletins, ensure everyone remains informed. Documentation, encompassing training records and incident logs, maintains accountability. Periodic reviews and adjustments to the program, influenced by lessons learned and regulatory changes, contribute to its ongoing effectiveness.